Design Engineering
- Home
- Design Engineering
From Concept to Reality
Our engineers are experts in bringing a napkin sketch to reality. Every design we work on is designed for manufacturability. We collaborate with you, as an extension of your own team – often as a more nimble way of moving a project forward quickly.
Deep manufacturing roots.
All of our engineers have deep manufacturing roots ensuring the products we design can be manufactured as expected. We utilize our nearly limitless manufacturing capability options to find the best material and process match for your application.
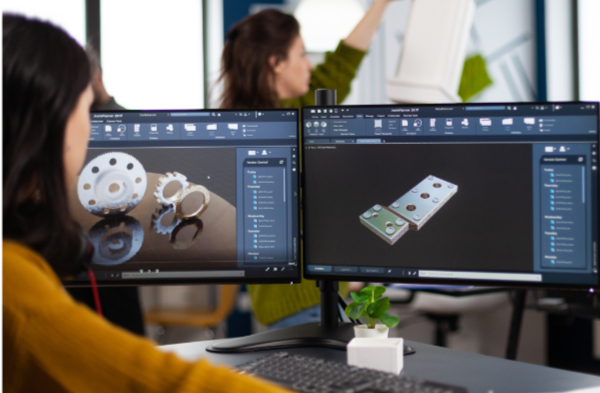
What we do:
- Define critical features
- Material selection (or create new ones!)
- Design for manufacturability
- Simulations to approximate real world results
- Hybrid prototyping for rapid development
Our toolkit includes:
- Mold Flow Simulation
- FEA (Finite Element Analysis)
- CAD & collaboration tools
- 3D printing and rapid prototyping
- Photo, video and augmented reality rendering.
Typical projects:
- Assembly & Sub-assembly development
- Metal to plastic conversions
- Sealing applications
- Tolerance stack-ups
- Prototyping and validation
OUR PROCESS:
Discovery
Design/Engineering
Prototype & Validation
Production / Lifecycle
Engineering for the next generation.
Radius partners with local technical colleges to provide scholarships, internships and capstone project opportunities. This allows students to apply what they learn in the classroom to real-world projects under the direction of Radius Engineers.
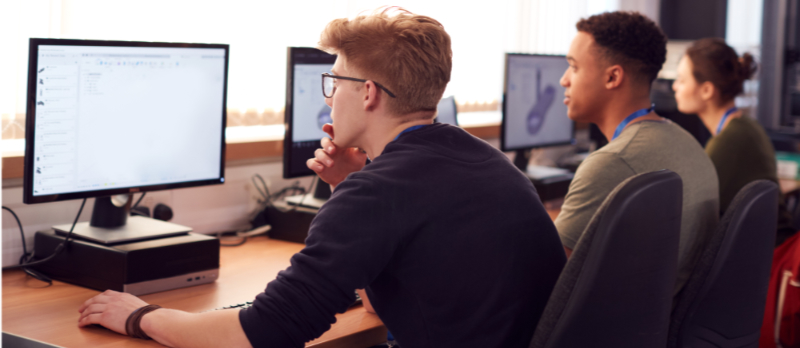
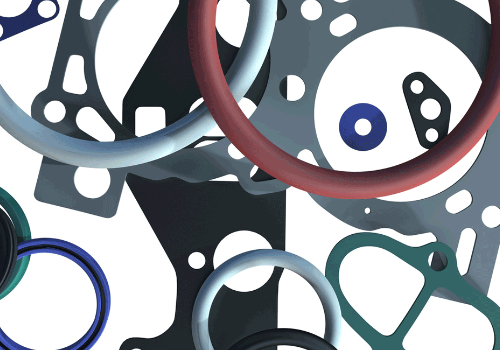
RUBBER
With a wide range of industry certified elastomers, reverse engineering capabilities and custom compound development, we specialize in tough sealing applications. If we can’t find the ideal material, we’ll create one!
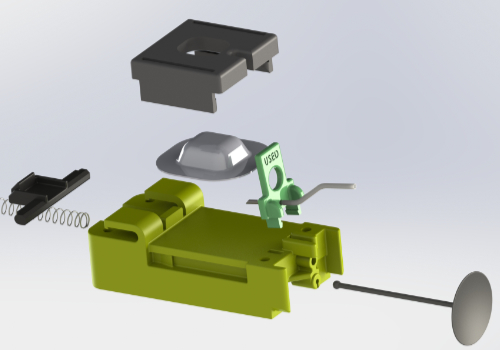
PLASTICS
High performance, custom blend or commodity resins are complemented by our wide range of press sizes (5 Ton to 3200 Ton) allowing for nearly limitless plastic solutions. We also specialize in metal to plastic applications.
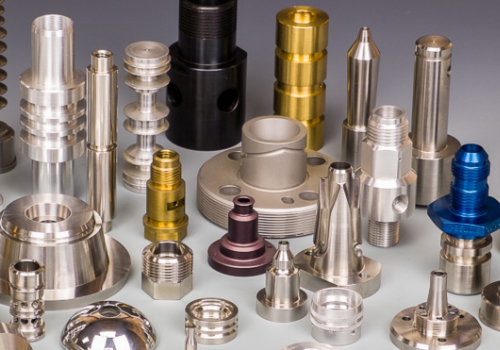
METALS
Radius offers a wide range of metal production options. Machining, casting, stamping and even Metal Injection Molding (MIM) allow us to consider the best process and material for your application.